The manufacturing processes of industrial heat exchangers have come a long way since their inception. From the traditional plate and frame heat exchangers used in the 1920s to the more recent brazed plate heat exchangers, technology has played a significant role in the advancement of heat exchange systems. The latest addition to this technology is laser welding pillowplate.
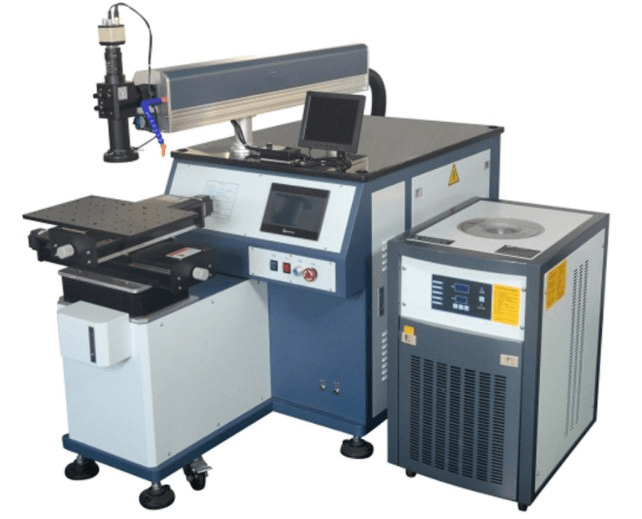
What are Laser Welding Pillowplates?
Laser welding pillowplates are the newest addition to the wide range of heat exchanger technologies. They are made by welding two sheets of metal using a CNC laser welding machine fiber. Pillowplates are designed to increase the heat transfer area of heat exchangers. They are customizable in size, shape, thickness, and pattern to fit the specific needs and requirements of each application.
Pillowplates are mostly made of stainless steel, but they can also be made of other metals, such as titanium and aluminum. This flexibility in material use makes pillowplates ideal for a wide range of industrial applications, including food and beverage processing, chemical processing, renewable energy, HVAC, and many others.
Laser Welding Technology and its Advantages
Laser welding pillowplates are made using fiber laser technology, which is also known as solid-state laser technology. It involves the use of a beam of light that is electrical and optic in nature, which is guided by a fiber-optic cable. The light is then focused onto a small spot, where it vaporizes the metal, creating a weld.
One of the significant advantages of using laser welding technology to create pillowplates is the accuracy and consistency of the welds. The technology is highly precise and automated, which means that the welding process is highly consistent, efficient, and repeatable.
Another advantage of laser welding technology is the ability to weld a wide range of material thicknesses, which means that the design of the pillowplate can be customized for specific heat transfer requirements. Laser welding technology also allows for the creation of complex geometries in the pillowplates, which can increase their efficiency and performance.
Why Choose Laser Welding Pillowplates?
Laser welding pillowplates offer several advantages over traditional heat exchanger technologies, including:
1. Enhanced heat transfer - The pillowplates' unique design allows for increased heat transfer, leading to improved efficiency and reduced energy consumption.
2. Easy maintenance - Pillowplates are designed to be easy to disassemble, clean, and reassemble, making them low maintenance and long-lasting.
3. Customizable - Pillowplates can be customized to fit specific requirements, ensuring optimal performance and efficiency.
4. Cost-effectiveness - Pillowplates are cost-effective due to their long product life and low maintenance requirements.
Conclusion
Laser welding pillowplates are the future of industrial heat exchanger manufacturing. With their increased heat transfer ability, low maintenance requirements, and customizable design, they are the ideal solution for a wide range of industrial applications. CNC laser welding machine fiber enables us to produce pillowplates with precision and accuracy, making them highly efficient and reliable. Whether you are in the food and beverage industry, chemical processing, or renewable energy, laser welding pillowplates offer unparalleled efficiency, durability, and effectiveness.